Saturday, October 22, 2011
Busy view
Today we started to put up the fascia boards, beginning on the west side. For this eave I connected two boards before putting them up because cutting them to meet at a rafter would have wasted a lot more wood. You can see where they come together. The caulk at the connection looks like a white scar with sutured stitches. It will be touched up when all the boards are in place.
I struggled with how Sandy and I could get the boards up and level them by ourselves. What worked was to clamp just one side of a joist hanger to some of the rafters with the other side hanging outside the rafter end. We then set the fascia board into the hanger and leveled it with shims. Screwing them in was easy then and didn't require a second person.
The 16-foot-long rafter visible to the right of the fascia is nailed to the top of the greenhouse wall and extends to the south side of the greenhouse over the foundation. The greenhouse wall will be built under it. In the mean time it is temporarily holding up a plastic covered, lattice like grid that can be seen to the left of the ladder.
Two doors are visible inside the greenhouse. The light one leads into the second bedroom; the other, to its right, into the living room.
The dark brown walls of the greenhouse are barn siding just as it came off the old barn. Of course Sandy cleaned every square inch of every board with a wire brush before I could use them.
The west end of the wall and the west side of the third bedroom still need siding panels installed.
Labels:
Construction
Thursday, October 20, 2011
A peek at the siding
I had hoped to use the siding from the barn we took down in a past life, but there wasn't enough of it for the entire house, so we chose siding like we put on the apartment. It looks good and is easy to install with a little help.
We painted it before it was put up. This has saved a lot of time. A touch up covers the nails after it is up.
Whatcha doing? |
Here's the first clerestory window with its siding and trim in place. The view is from the front of where the greenhouse will be.
Labels:
Construction
Another climber
Though not as helpful as Lucas, I spotted another local resident who apparently likes to climb. On my walk from the apartment to the house one morning, as I got to the rain garden Sandy created, I noticed something unusual at the top of a three-foot-tall lobelia and stopped to check it out. Here's what I found.
This little guy was about 10 inches long and wrapped three times around the very top of the plant. Each of the next two mornings it was still there, but was gone by the afternoon of the third day.
If anyone can identify it, please post a comment and I'll update this entry.
Labels:
Critters
Finally catching up
Once again there has been a big pause in posting activity, but the work has gone on. Here's a partial rundown of where we are on various parts of the project.
All three bedrooms' walls are finished - drywalled, taped, mudded, primed and finish painted. After the floors are stained the trim will be added.
The second bedroom's loft frame is in place and ready for its floor.
The hallway, living area, "office" and kitchen areas are also finished and ready for the kitchen cabinets and pantry. They, too, will have stained floors, and after that, the door and widow trim.
All electric wok is done except for wiring and hanging lights, most of which are now purchased.
Other than the plumbing and electrical stub-ins, the bathroom and half bath are yet to be finished. Floor tile, glass block, tub, sink and vanity have all been purchased and are awaiting installation after the tile is laid.
About 80% of the outside wall is now covered and painted - two coats.
Window and door trim has been cut, painted and installed for all windows where the siding is up.
The bead board for the eaves across the front has all been painted and is ready to go up when the lookout rafters are installed.
The greenhouse area has a very temporary roof on the north half of it and the old barn siding has been cut and installed on the inside of its north half.
Lots of work has been done on the hillside in front of the house, including about half of a stone stairway that climbs the hill to the house. A stone walkway has been started leading from the front door toward the parking area.
Sandy and my sister Judy (who came out from Delaware to help for more than two full weeks) have worked relentlessly to paint and help put up the siding among other things. Each spent at least a week in a row doing almost nothing except painting, either while hunched over 4 X 8 sheets of siding and bead board before it was installed or up and down a ladder painting drywall after it was up.
I'll post a bunch of pictures next that cover much of what is listed and some other topics.
Labels:
Construction,
Outside projects
Wednesday, August 24, 2011
Greene View Springs official best tree climber
When the small tornado knocked the closest tulip poplar into the east wall of the house, I trimmed the top out of it and, with Brian's help and a come-along, we pulled it back up and braced it.
It seems to be growing well but I was never able to get the strap down from the top because the branches are too small for me to climb. Enter Lucas...
With a little encouragement, he climbed to the top and disconnected the strap and the protective wrapping. What a guy!
Summer activity
Once again it's been a long time since the last post. Work continues at the pace of 8 hours a day more or less for me mostly, inside, plus a few hours or more most days for Sandy, mostly working outside, in the heat, moving soil to the front hillside and grading the entryway at the front door. The heat has been oppressive for weeks now, so one can only work at most 30 minutes at a time outside.
Inside the temperature had been up to 20 degrees lower inside (low 70's) but the humidity was above 80% all the time. It was so bad we began to find mold on drywall and doors, especially areas that weren't well ventilated. Our small dehumidifier was able to drop the humidity in one of the bedrooms at a time, but had no effect in the larger areas. We purchased a Kenmore unit that is rated at 70 pints a day and it brought the humidity in the entire building down to 50% (where we set it) within a few days. Though the indoor temperature in now in the high 70's, the humidity throughout is hovering at 50% and it feels great coming in from outside.
I don't find hanging drywall, taping, mudding and applying a primer coat as worth showing in a post. When the walls are all done I'll post a video walk-through.
In July we took two grandsons back east and visited my son in Maryland, my sister in Delaware and Sandy's uncle and aunt in Ohio. On the way home we brought my granddaughter from Maryland who stayed with us for a week. Then my other son visited from North Carolina with his two who live in Germany. They stayed a few days and I went back to Durham with them for a week. We all then went back to Maryland to take the Maryland granddaughter home. She is only seven and she was away from home for over two weeks. What a gal!
There was virtually no time for work the short week I was home in mid July. All that got done was getting two heavy wires pulled through the tube in the floor for the oven and stove top.
Oh yeh, and I got some help painting.
Audry paints the first wall, in the smaller bedroom
while Lucas and Kira work on another.
Labels:
Construction,
Family,
Fun
Sunday, June 12, 2011
What happened to May?
I just realized I haven't posted for over a month. A lot has happened so I'll just show some pictures taken at various times since April.
Damaged tree
We lost a bunch of trees in the tornado. The large one that hit the new house will be the most missed as it was right in the line of sight from any south-facing window. It had split in two at a vee about 30 feet high, spun 180 degrees and the south half fell north onto the house. The rest of the tree was doomed so it had to go. Here's the view soon after the damage and then after the tree was removed.Bedroom progress
A lot of drywall has been put up. Here's a view of the master bedroom from the kitchen area.Pond planting
Sandy got a few water lilies for Mother's Day and enlisted Brandon and Matthew to help her place them in the larger pond below the house.Morning surprise
Completely unrelated to the new house, I found this luna moth on a window when I got up the other day.After dark I coaxed it out the apartment window and it just glided to the ground outside. It hadn't moved for five minutes or so, so I went downstairs to see if it was alive. As I tried to pick it up, it took off and flew away.
I looked them up on the web to find out the adults only live about 8 days. They have no mouths and spend their entire adult lives trying to reproduce.
Labels:
Construction,
Critters,
Flowers,
Trees,
Views
Wednesday, April 27, 2011
We heard the freight train...
just like people say it sounds as a tornado goes by. It was followed by a loud crashing sound. I got Sandy up and we went to the first floor for safety. That was about midnight.
When the storm was mostly over I went outside in the rain to see how bad it had been. Up to that point I thought it was just a really nasty storm.
That's when I noticed a large metal locker at the end of the walk and a trashcan on top of a whiskey barrel planter. Both had been about 20 feet away under our carport. Obviously something was wrong with that picture.
I looked around the corner to find our carport crashed on top of the Buick. It had been lifted right out of the ground. The carport contents were strewn all over creation.
Part of the white tarp that was on top of it is in the top of a tree about 100 yards away looking like a giant ghost.
We called 911 to report the damage. About 1:30am a sheriff's deputy came by to be sure no one had been hurt.
He reported the tornado had moved two cars parked at a nearby house and damage had been done to the house across the county road from the new house. Also power lines are down on the road by the new house. We lost power at the apartment for about an hour.
There doesn't appear to be any damage to the apartment though it did suck open the bathroom window and then closed it again on the curtains which were then hanging out in the rain.
In the morning I took lots of pictures both at the apartment and then down at the new house. There was no damage there except the entire floor of the building was covered with muddy water at least an eighth of an inch deep. A door had blown open and apparently the wind had roared through the building.
Many trees were down, both on our property and across the county road. Two fell all the way onto the front of the house but incredibly did no damage. The very tops of the trees were leaning against our new windows without even a scratch on the frames.
Two of the panels on the rafter extensions were missing and one was damaged. I found one of the panels had just flipped over onto the roof, still connected by the flashing. The other was found behind the house about 70 yards from where it started.
Here's a link to the pictures.
When the storm was mostly over I went outside in the rain to see how bad it had been. Up to that point I thought it was just a really nasty storm.
That's when I noticed a large metal locker at the end of the walk and a trashcan on top of a whiskey barrel planter. Both had been about 20 feet away under our carport. Obviously something was wrong with that picture.
I looked around the corner to find our carport crashed on top of the Buick. It had been lifted right out of the ground. The carport contents were strewn all over creation.
Part of the white tarp that was on top of it is in the top of a tree about 100 yards away looking like a giant ghost.
We called 911 to report the damage. About 1:30am a sheriff's deputy came by to be sure no one had been hurt.
He reported the tornado had moved two cars parked at a nearby house and damage had been done to the house across the county road from the new house. Also power lines are down on the road by the new house. We lost power at the apartment for about an hour.
There doesn't appear to be any damage to the apartment though it did suck open the bathroom window and then closed it again on the curtains which were then hanging out in the rain.
In the morning I took lots of pictures both at the apartment and then down at the new house. There was no damage there except the entire floor of the building was covered with muddy water at least an eighth of an inch deep. A door had blown open and apparently the wind had roared through the building.
Many trees were down, both on our property and across the county road. Two fell all the way onto the front of the house but incredibly did no damage. The very tops of the trees were leaning against our new windows without even a scratch on the frames.
Two of the panels on the rafter extensions were missing and one was damaged. I found one of the panels had just flipped over onto the roof, still connected by the flashing. The other was found behind the house about 70 yards from where it started.
Here's a link to the pictures.
Labels:
Weather
Tuesday, April 26, 2011
Rock walls
Now that the trencher, the last heavy vehicle that needs to get behind the house, is finished and gone, we can start getting the east-side hill they way we want it to stay. Sandy got a shot of me moving a large rock for the retaining wall. There are lots of rocks on the property much, much larger than this one.
The wall should look lots better when we get some plants started on it. The rocks on the right are steps to get onto the hill. The wall will be about eight feet longer.
Labels:
Construction
More progress
All of the interior doors are now in place. Here's a look at two of them through a framed wall in the second bedroom. The left one is in the third bedroom. They both lead to the half bath.
And I finally have electricity where it should be: at the breaker box in the utility room.
Here's the meter box awaiting it's hookup by the power company. They came the next day.
The nearly level area behind the house is a result of hours of work by Sandy after the power line was buried.
Before the contractor filled in the trench I was able to drop in another drainage line to take runoff down the hill to the east toward the driveway.
Labels:
Construction
Letting in the light
Above the master bedroom and the bathroom walls on the hallway we are installing windows so light from the clerestory windows can brighten them too. There's not a lot to see yet since the windows haven't been stained or painted, but here are two pictures.
The first is showing one window's wall being framed. It will go in the top part of the bedroom wall.
And here's a look at the bedroom walls from inside the bedroom. The two sliding doors on the right are to the left side of the closet. The pocket door looks into the hallway.
Labels:
Construction
Friday, April 1, 2011
The bituthene stomp
Over the last week the "roofing crew" has developed a new dance. Its purpose is rather mundane - tamping down seams between strips of the roof membrane to get a good seal, but its implementation can be entertaining.
We used a product called bituthene which comes in 66-foot rolls that are 36 inches wide. They require an overlap on the edges and ends as they are laid down in shingle fashion from bottom to top. Lines on the edges of the strips aided in alignment, but it took a number of strips before we found a placement method that produced the best results.
We learned that it was counter-productive to try to run a single length of the material all the way across the roof. Unless we started out precisely straight with the roof and with the previous strip, the slightest angle off caused the line to veer further as we went along. This would cause an insufficient overlap which had to be corrected with a short overlay, and this is not best since the shingle effect is lost where the overlay covers both strips. Consequently, we chose to limit each strip length to no more than about 12 feet.
We had to put the membrane down carefully to be sure we got the required overlap and to prevent creases from forming. This took a crew of three: one to hold the whole strip off the surface and let it down slowly and evenly, one to wrangle the paper backing and one to press the membrane down smoothly. Near the end of each strip the first two shared their duties as the remainder shortened.
On each side of the membrane roll there is a very narrow strip that is not covered and is very sticky, like the bottom surface. Once a strip was in place, and while the next was being cut to length, two people were free to stomp the seams. This was done using the backing paper that had been removed since one side of it does not stick to the membrane.
Weather was a factor. It rained a number of times before we were finished. Each threat of rain required us to recover the roof with our trusty billboard tarps. And after each rainfall we uncovered the roof again and found something else to work on until we were sure it was dry. Fortunately, the rainy weather also brought windy days so the drying off time was shortened. Overall it took about eight days to finish the job, though few of them were full ones.
Surprisingly, after all the miserable weather we've had the last month or so, I found myself hoping for cold weather to place the membrane since it was far less sticky when it was cold. Cloudy days were welcome.
The pictures below show the process, the "dance" and the roof covered with the membrane.
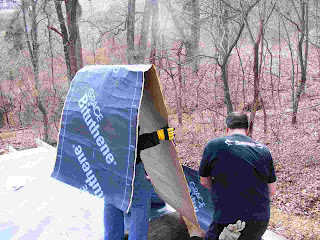
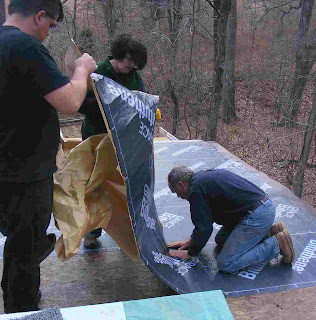
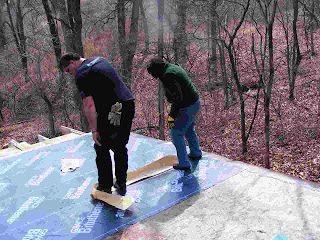
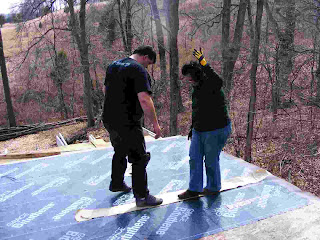
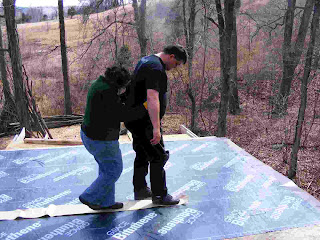
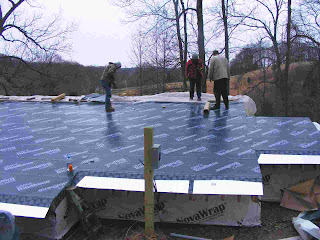
Labels:
Construction
Tuesday, March 29, 2011
Still here
I realized tonight there have been two primary reasons/excuses for not posting more regularly over the last four months or so.
First reason: I don't post much when there is nothing new to tell or no progress overall that I find to be newsworthy.
This reason covers much of the late fall and early winter. It took much longer than I had hoped to get the final drawings to the SIP manufacturer and, consequently, the panels weren't ready until after Christmas. This, combined with the weather-affected schedule of the installers, left us without a reliable roof until early in January. No roof in winter, no inside work, no news to post.
Second reason: When we can work, I have to choose between the work and documenting the work.
Some days, after the roof was put on, I worked until 8 PM, and sometimes later. By the end of one of those 10-hour-plus workdays, I just don't have the enthusiasm for sitting down to craft a meaningful entry.Also, when there is help for things that take more assistance than just Sandy can provide, we try to work long days because the extra help usually isn't here for too long at once. Neither situation leaves a lot of time for documenting what's being done.
Since the last post in early February, the windows and doors have been installed, 98% of the interior walls have been framed, lots of building materials have been purchased and moved in, and a dishwasher, kitchen sink, faucets, bath tub, second-bath sink, vanity and toilet have all been purchased and moved in. Finally, all the materials for the waterproofing layer of our living roof were purchased and picked up.
The plan was to keep the SIP roof covered until we had close to a week of dry weather to install the waterproofing. (Based on our weather lately, I began to fear that would be late July.)
But two weeks ago my sister Judy came from Delaware to help. She left for home today, but while she was here she worked long hours with me and we got more done than I could have in two months. The most significant accomplishment was to get all of the waterproof membrane installed, a three-person job.
I didn't take any pictures, but Sandy did and over the next few days I'll try to get them posted.
Labels:
Construction
Sunday, February 6, 2011
Holy Owl!
We've had a few days of fairly decent weather (compared to the last two weeks anyway) so, with help from grandson Nick and from Brian, we've gotten most of the clerestory windows framed and covered with house wrap.
Saturday, after working in the house with power saws, pneumatic brad nailers and lots of hammering, Brian happened to look up to see which panels next needed to be tacked up and said to me, "What's that?"
It was this little screech owl.
Who, me?
He or she spent the rest of the day in the house, occasionally flying between beams until finally settling in the farthest northeast corner. We kept working as if the owl weren't there. Our only concession was not working where he was in the bedroom until Sunday.
At the end of our day, when the owl's was just beginning, it flew to the east clerestory window opening and sat on the roof for a few minutes. Next time I looked that way the owl was gone. Is that cool or what?!
This morning we got down to the house soon after 9 and there it was again, sitting on the same beam it started on yesterday. In addition there was a pile of feathers from something the owl ate under a beam closer to the window.
I couldn't tell what kind of bird it had been. The feathers were too long, too dark and too many to have been one of the smaller over-wintering birds.
Soon Brian was finishing up with the brad nailer in the bedroom area, so the owl flew into the closet. Brian kept working, at one point just five feet from the owl. After that area was finished and Brian had moved away, it flew again to the far back corner where it spent most of the rest of the day.
It left silently about 5 pm. Can't wait to see if it's back tomorrow. The openings are much smaller now than they were this morning. As I was nailing the easternmost window's frame I noticed on some of the interior bracing between wall studs "proof" that the owl has been in the building more than we knew.
Here's a look up through the greenhouse area at the clerestory window opening in the 2nd bedroom. The panels still need to be caulked and have house wrap applied. After that, and the same for the other three windows, and we will start installing windows and doors.
Today the temperature got enough above freezing to allow pushing the snow off the front roof which made closing in the window openings possible.
The weather forcast includes snow and some single-digit temperatures, so we may still be days away from finishing the windows. I can't work on the roof if it's covered with snow and I can't caulk the seams from the inside or if it's below freezing.
There are plenty of other projects inside, so things will keep moving, but it will sure be nice to have the windows and doors in so we can add a little heat on these cold days.
Labels:
Construction,
Critters
Tuesday, January 25, 2011
Up On the Roof
When this old world starts getting me down
And people are just too much for me to face
I climb way up to the top of the stairs
And all my cares just drift right into space
On the roof, it's peaceful as can be
And there the world below can't bother me...
"Up On The Roof"
(Gerry Goffin and Carole King)
Finally, we have a roof. It's seemed like an eternity, but our roof is in place after two more days of moving panels, prepping them and lifting them into place, Jerry Ellis' crew has slid all the panels into place and screwed them down to the rafters. It was quite a struggle so this post might take a while...
Actually, most of the struggle was with the weather. About three inches of snow fell on us last week so we postponed the second truckload of panels until Monday. We had covered the entire roof with long sheets of plastic that ran up and down the roof slopes.
The plastic had been removed from the two south-sloping roofs (not shown) and the easternmost section of the north roof. There were still many snow-covered square feet to go.
The south-facing roofs' SIPs were placed by the end of the day, but I'm getting ahead of the story line.
The previous post discussed the problem we had getting the loaded truck into the driveway. In preparation for the second load, last week we shoveled the driveway, and helped by two days of on again-off again rain, most of the snow was gone. Then the driveway was covered with tarps to protect it from the predicted snow. On Sunday Sandy and I shoveled and pushed the snow off the tarps and dragged the tarps themselves off the driveway. Once it was all cleared we dragged the tarps back on because yet another snowfall was predicted.
That snow came Sunday night but was fortunately just enough to cover the tarps but not hide them. On Monday morning I dragged the tarps off the driveway again and spent a half hour or so shoveling and scraping the county road at the end of the drive.
The crane arrived and was set up at the house and we waited for the second trailer-load of SIPs. By the time it arrived the installers were also in place and we all went down to the road to see if the truck could get in. Even as the driver stopped on the road above the driveway, the truck slide a few more feet downhill. He was not very optimistic that the truck could back the trailer into the drive. It wasn't a really large truck, but a larger one, pulling a trailer, could not make the required turn.
As the driver was about to pull down the hill past the driveway so he could back it in, it occurred to me there might be a possibility he could just pull it in straight, so the drive wheels would be on gravel when the trailer came off the road. I checked with the crane operator to see how far the truck would have to get and be sure there was enough room at the end of the drive to get there.
We concluded that it might work and that it had a better probability than backing in, so we went for it. After a few tries and more than a few back-ups for aligning the trucks wheels, the truck had pulled forward enough to be reached by the crane. Success!
Next began the process of lifting the panels from the trailer onto the "lawn" area. This took longer than we'd hoped because the panels come in bundles and the bundles are mostly too heavy for the crane we had so they had to be "broken" on the trailer and the panels moved one or two at a time.
When this second load was off the trailer we took three trailer trips back to the end of the driveway to bring the rest of last week's first load up to the house. On the first two trips panels were loaded by brute force. By the third trip the panels were too low to the ground and too heavy for four of us to lift by hand, so the crane had to be moved down the driveway to load the trailer and then moved back into place to unload it onto the piles of SIPs.
Finally, a half hour past noon or so, we were ready to start lifting panels. So we took a lunch break. ?!
The panel on top to the right is just sitting there waiting its turn.
The holes that can be seen in the sides of some of the panels on the pile are where the nozzle is inserted to pump in the insulation. Between each hole is a thin black line that shows where the segment dividers are. There is a small number at each hole that tells the machine operator how many seconds to leave the nozzle in for that particular segment. Pretty slick, eh?
The two south-side roofs were completed on Monday.
This view shows the second bedroom above and the larger bathroom to the right. There will be a wall between them of course.
And finally, here's a view from an angle that hasn't been shown in any previous posting, looking through the trees to the east of the house. The panel in the air is the last one to be installed. A few minutes later the roof was all in place.
Finally the ball is entirely in our court. Much is left to be done, but it can now all be done on our schedule. Doors and windows will be delivered on Thursday.
Labels:
Construction
Saturday, January 15, 2011
Not quite what we'd hoped for
Friday was to be the big day - the day our SIP walls and roofs were to be installed. It started out fine: The crane arrived and the operator set it up right near the building; the trucker called to say he was loaded up with panels and on his way, and the installers arrived and unloaded their equipment. We all waited for the truck to arrive.
On Wednesday and Thursday Sandy and I had begun placing the paneling that will hide the bottoms of the roof SIPs. (Think of them as really thick wall paper.) We couldn't start earlier due to nearly two days of snow, much of it still covering our entry road. There were still a lot of panels to put up and we hoped we could get them done fast enough to keep ahead of the SIP installation.
Soon the truck and trailer arrived on the county road, went just past our drive and began to back uphill into the driveway. He was unable to get enough traction to get started into the driveway. Then he drove south to the end of the road and turned around, hoping that, by heading uphill, backing into the drive would be possible.
To make a long story short, after a few slippery tries back and forth, we ended up with the rig cross-ways on and completely blocking the county road and unable to move either way without slipping all the way into the ditches on BOTH sides of the road simultaneously!
Eventually a wrecker was called to pull the rig uphill and open the road. In the mean time, the crane was relocated to the end of the driveway, just off the road, and all the panels were picked up and moved onto the small parking area there. Then the panels that could both fit and be lifted manually were loaded onto the crane and driven to the house.
The last three wall panels were too large to move on the crane so they are still waiting near the road under a tarp with a half dozen of the roof panels until the driveway can be maneuvered by the truck and trailer. (Our plan is to break up the snow and ice, cover the driveway with tarps and hope the sun will melt it dry under the tarps.)
The rest of the day was spent mounting the wall panels that were moved up to the house. Here's a view of the crew installing the short wall behind the office space.
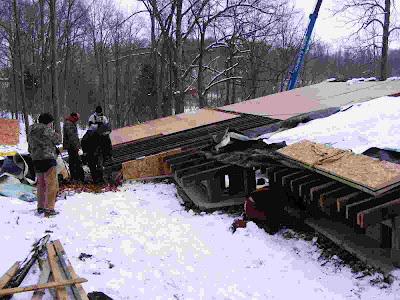
While the installers worked on the SIPs, and with the help of our grandson Nicholas, I continued placing and tacking the panels into place.
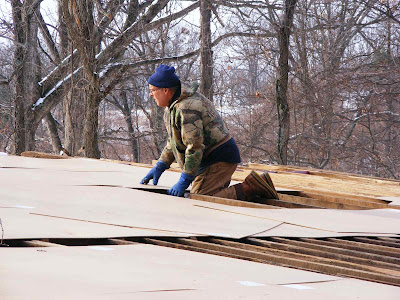
The only upside of the truck-on-the-slippery-driveway fiasco was that we were no longer under extreme time pressure to get all the under-the-SIPs panels in place. Obviously the truck did not go back for the second load so the roof would not be finished this week.
We finished the roof paneling installation Saturday and began covering the panels with plastic in expectation of the snow and rain predicted for next week. Our installers cannot come back until at least Thursday, and more snow is predicted for that day, too, so we don't know when the job will be done. Thursday is the soonest possible, and only if the driveway is not frozen and we can get a trailer in to the house.
With most of the exterior walls now in place, after getting all the plastic up tomorrow, and if there isn't enough wind to whip off the plastic, I'm hoping to get some interior work started.
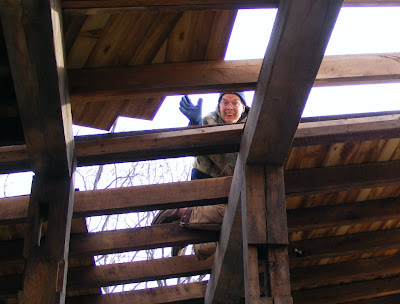
Bye for now.
Labels:
Construction
Thursday, January 6, 2011
Bummer!
For about a month, the installation of our SIP panels was scheduled for this Friday and Saturday, the 7th and 8th of January. Last week I called the installers to verify that we were still on for those dates and got a "Yes."
I then called the manufacturer to assure them the SIP panels would be picked up on the 7th, the truckers to verify we were still on their schedule, and the crane company to be sure we could unload and lift the panels into place. Everyone was on the same page.
My plan was to use this week to remove the tarps and put up the paneling that will show above the rafters and under the SIPs. (See post showing panelling.) The weather forcast was good - either clear, or well below freezing, so any precipitation would be snow, not rain.
Monday morning we got a call saying the installers could not be here this week and they had to put us off until the 14th and 15th!
What could we do? Nothing! Too late to schedule anyone else, if there even is anyone else nearby with the experience (and availability) to install the SIPs. I called the other three participants in the venture - manufacturer, trucker and crane operator - and verified that a week later would work for their schedules. Fortunately they all said it would.
So, instead of getting ready for the SIPs this week, I am using the week to remove the tarps and spread them on the ground so they might warm up a tad and be more supple when they are replaced over the SIPs next weekend. Next, after the projected snow showers today and tomorrow are over, I'll start lifting and fastening the panels and hope for the best (no rain, but not too far below freezing) for the rest of next week before the panels go up.
I'll post a picture when all the panelling is in place.
I then called the manufacturer to assure them the SIP panels would be picked up on the 7th, the truckers to verify we were still on their schedule, and the crane company to be sure we could unload and lift the panels into place. Everyone was on the same page.
My plan was to use this week to remove the tarps and put up the paneling that will show above the rafters and under the SIPs. (See post showing panelling.) The weather forcast was good - either clear, or well below freezing, so any precipitation would be snow, not rain.
Monday morning we got a call saying the installers could not be here this week and they had to put us off until the 14th and 15th!
What could we do? Nothing! Too late to schedule anyone else, if there even is anyone else nearby with the experience (and availability) to install the SIPs. I called the other three participants in the venture - manufacturer, trucker and crane operator - and verified that a week later would work for their schedules. Fortunately they all said it would.
So, instead of getting ready for the SIPs this week, I am using the week to remove the tarps and spread them on the ground so they might warm up a tad and be more supple when they are replaced over the SIPs next weekend. Next, after the projected snow showers today and tomorrow are over, I'll start lifting and fastening the panels and hope for the best (no rain, but not too far below freezing) for the rest of next week before the panels go up.
I'll post a picture when all the panelling is in place.
Labels:
Construction
Subscribe to:
Posts (Atom)